The following is an article adaptation of a presentation called “The Effective Automation of Things” presented by Rob Boyd, Head of Product Management at Schleuniger, at the EWPT Expo in Milwaukee on May 16. In his presentation, Rob discussed the reasons to automate and how best to assess application feasibility. He reviewed challenging applications from the harness industry, common mistakes in automation and stressed the importance of creating specifications when automating a process.
Why Automate?
Back in 2018, The primary focus for automation was on cost reduction, improving productivity (including the reduction in the scrap rate), and reliability. While these remain key factors today, the shortage of labor takes the lead role in the justification for automation. This does present a double-edged sword as operators for automated equipment require a higher skill level and generally take longer to train.
Several advantages of automation emerge as volumes increase. Merely allocating more staff to handle higher volumes is inherently problematic. People tend to lose focus. They get distracted and lose momentum. That increases scrap rate but, more importantly, it becomes a safety concern. Repetitive motion injuries alone are a huge issue in manual assembly.
As assembly becomes too complex for humans, automation becomes more attractive. This is especially true in dangerous high-voltage and high-pressure applications. As precision levels increase, it becomes more difficult for humans to perform tasks. A machine can most often achieve much higher tolerances.
When the cost of failure is extremely high, the consistency offered through automation becomes very attractive. For high reliability applications, it’s best to remove the human element wherever possible. Automation provides a much greater degree of traceability. One classic example would be airbag fabrication.
In general, machines give us a much greater ability to collect and share data. With this data, we have a much better idea of what is really happening on the manufacturing floor. In real time we know what our throughput is, what our set up times are, and where we are falling short.
Application Feasibility
The first place to start in ascertaining the feasibility of an automation application is to have a 100% understanding of the process. Do the parts fit together easily or is an operator needed to make on the fly adjustments? Ascertaining the key quality points is essential to success. A good rule of thumb is that the automation of the process should be 80% “known” (or at least understood) as to how it will be done, allowing for 20% of imponderables that may pop up.
For wire processing automation the first thing to look at is the cable construction. For example, flat cable is obviously much easier to work with than round cable. But flat cable with a shield and molding can get complex very quickly. Automated processing of round cables with fillers and shields and foils can also be very complex. Overall, the easiest applications to automate are where the cables are symmetrical.
When analyzing a complex application, a feasibility study is strongly suggested. Many automation houses will generate simple jigs and fixtures, or even generate 3D printed parts to develop various approaches to automate the application. It can be expensive but It’s an option to be considered for those processes that are really questionable.
Automated Testing
There are a variety of test applications that can be automated. Things like pin height, connector coding/recognition, pressure, resistance, continuity, and various visual inspections can be integrated into the automation process.
Challenging Applications
The biggest challenge in wire and cable assembly automation is in dealing with inconsistent materials or parts. It could be the inconsistency of insulation thickness, the wrap or the conductor itself. Often the biggest issue is with the variability caused by wire memory. Variations in the bend of a wire for example, may be different depending on which part of the reel it comes from and presents a challenge in orienting wire on a consistent basis.
As things get smaller and smaller, automation challenges become greater. A multi conductor wire being terminated into a fine pitch connector is an arduous task. Terminals that come as loose pieces or with an odd shape will be difficult to orientate for processing. Wires with high strand counts can also add challenges in an automated system.
Overall, higher quality parts are easier to work with in the automated process. Obviously, there will always be pressure to seek the most economical choices with individual components in an assembly. It is imperative, however, that lower cost parts stay within tolerances because the machine is expecting consistent dimensions every time.
Closed barrel applications are particularly challenging. Wire memory is again the main culprit. There needs to be enough clearance between the connector and the terminal so that the conductor can slide in easily. With limited clearance, the operator needs to make gentle twisting adjustments to fit the wire into the terminal. Such a scenario may be a bad candidate for automation. Schleuniger recommends adding funnels to applicators in closed barrel crimping wherever possible (fig. 1).
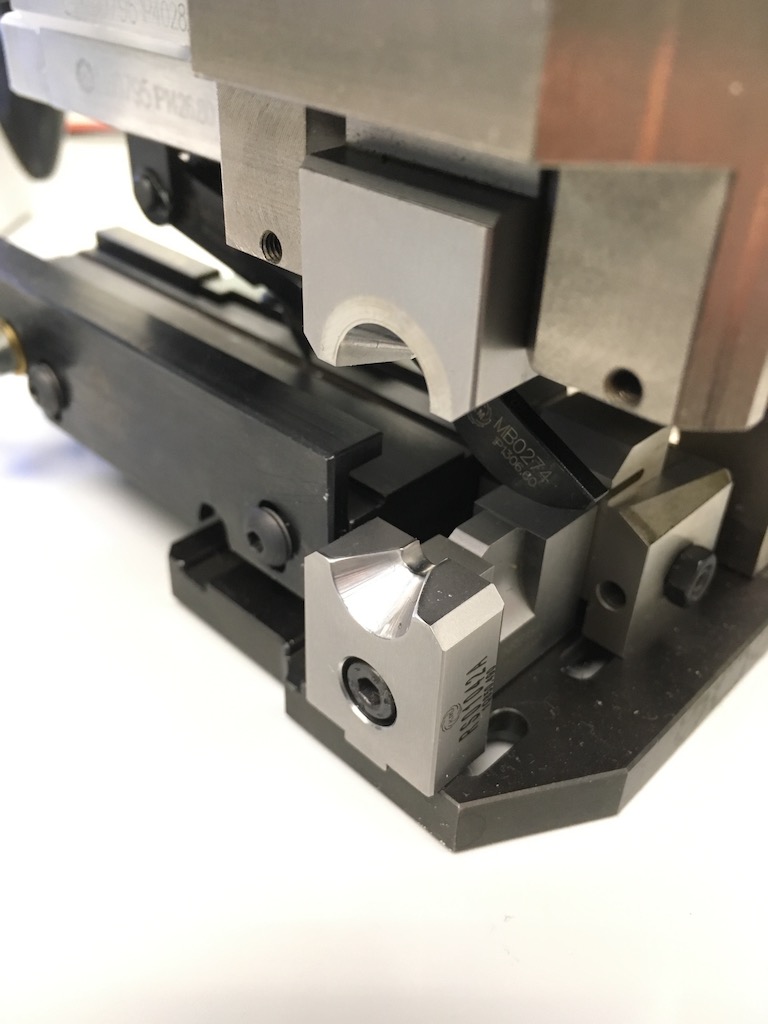
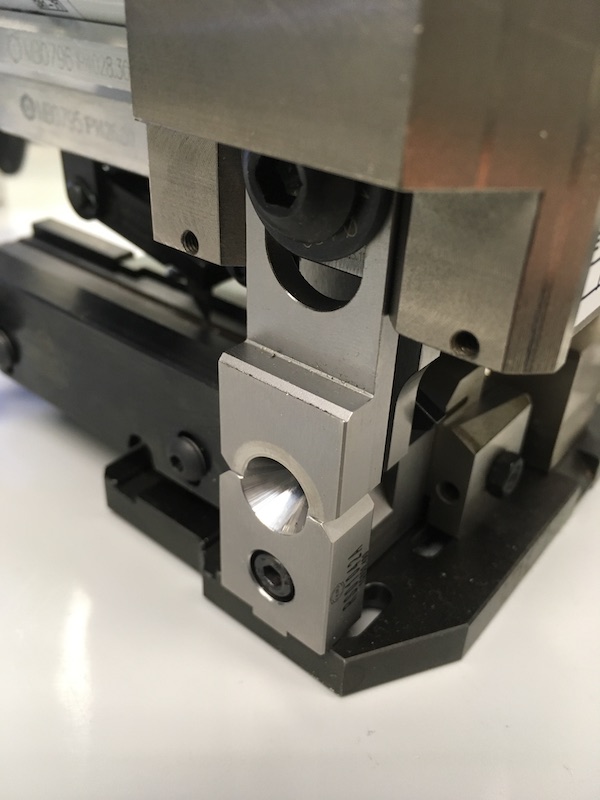
Figure 1. Funnel installed on applicator.
With a bigger target, there is much more flexibility. Often, manufacturers of pre-insulated closed-barrel terminals will offer two series of the same terminals: one for bench-top applications, and one for automated equipment.
Short breakouts, where the distance from the insulation to the end of the conductor is minimal, are also quite difficult. Figure 2 shows a cross section of an applicator with a wire ready to be crimped in an applicator. Ideally you need considerable room for the tooling, gripper and shield to complete the crimp process. When that room is limited, challenges arise. Similar issues arise with multi-conductor connector configurations.
Common Mistakes & Misunderstandings
The most common misunderstanding in automation is that machines are better at everything. Humans still hold an advantage over machines in many ways. We are much more tactile and can feel strands and fine grains that sensors cannot. Vision cameras just don’t have the resolution of the human eye and cannot distinguish as well under variable lighting conditions. AI is growing leaps and bounds in terms of reasoning and decision making but is not quite there yet.
Another stumbling point is the notion that machines can take bad parts and make them good. As stated earlier, you have to be willing to pay a little more for quality parts as they will run better in an automated system.
Many folks think that if they can run more parts from a particular automated system, it will justify the cost. They erroneously assume that fully automated equals fully flexible. Systems today are becoming much more flexible, but a typical large transfer line can only run two cable sizes per machine. Test automation is a bit more flexible and can usually run three variations.
Overall Equipment Efficiency (OEE) gets a lot of attention these days. Many assume adding automated equipment will boost OEE to 95%, but OEE is a fickle thing. An OEE of 80% is considered world class. An OEE of 60% is more typical in manufacturing and provides a good baseline for improvement.
Many manufacturers embark on a new project without fully understanding the basic requirements of the process being automated. It is imperative to know the quality requirements, understand acceptable defect rates and have a clear picture of future output needs before approaching an equipment vendor. Only then can you make a sound ROI analysis to decide if automation is the right choice.
Not every application is suited for automation. Some jobs just run better on bench-top equipment. Design for manufacturability should be considered when designing a high-volume assembly. It might be better to use a connector with better orientation characteristics that make automation more feasible. Overall, simpler designs reduce costs.
Creating Specifications
The first step in designing an automated process is to create a detailed document outlining the basic user requirement specification (URS). There is no rule on the length of the document as long as it’s inclusive and collaborative. The URS should encompass the full assembly process (up and down-stream) with workflow instructions. A good URS details quality requirements, production and delivery schedules and has a firm grasp on product life cycles. It should also consider the labor and skill level required to implement an effective automation process. As mentioned earlier, automation typically requires employees with a higher skillset to run and monitor the equipment and the learning curve can be much higher than manual processing.
It is prudent to keep things focused and as simple as possible when creating a specification. Enhancements can destroy timelines, create general frustration and kill a project. There is often temptation to begin by automating every process. It is better to start small with the processes that are most critical to the organization.
In summary, there are many reasons to automate. Using quality materials, focusing on key processes and understanding requirements are critical to the mission. Open communication between the automation vendor and your own employees will produce meaningful results.
For more questions on automation in wire processing, contact Rob at robboyd@schleuniger.com.
Article was published by Wiring Harness News.