The automotive world is swiftly changing, with a shift to higher efficiency hybrid, electric, and even alternative fuel vehicles. Automotive engineers have turned to Techflex® for decades to collaborate on protective OEM wire harness solutions — and continue to depend on Techflex® for its expertise in safeguarding the cables on their state-of-the-art vehicles.
While standard gas-powered cars and trucks have always benefitted from wire protection, EVs and other automobile types are comprised of a greater number of electrical systems. That wiring and circuitry call for additional safeguards. Techflex® is recognized as a sleeving solutions authority, manufacturing and engineering numerous categories of this useful cable organization product, to suit diverse wire coverage needs. Braided sleeving is an ideal wire management tool because it maintains flexibility as it navigates a vehicle’s complex structure.
Whether driven in Alaska or near the equator, these modern vehicles universally face the same challenges because they operate with delicate electronics, colossal batteries, radar, temperature monitoring systems, and a multitude of sensors. Wire harnesses for these systems are vulnerable to threats of all kinds if left unprotected. While braided sleeving organizes automotive wires, it is frequently applied in the vehicle manufacturing process at the harness assembly phase. As we demand higher and higher performance from our vehicles, there are a greater number of needs for protection in every automotive system.
Protective Solutions for Groundbreaking Vehicles
The electronics in higher efficiency hybrid, and fully electric vehicles are intricate, as they are designed to achieve optimal environmental friendliness and reduce noise pollution. It can take multiple motors and batteries within one of these vehicles to operate its myriad of cutting-edge electrical systems. As each manufacturing milestone occurs, automotive engineers frequently team up with Techflex® to develop novel ways of improving wiring protection technology. For example, one of these synergies resulted in creating a composite solution of fiberglass-infused braided sleeving. Special impact resistant coatings on sleeves were another combined effort between Techflex® and a vehicle manufacturer. Techflex® has also customized sleeving per manufacturers’ specific requests, conceptualizing exclusive colors, special wall thicknesses, and other engineered solutions for OEM applications.
Techflex® protection technologies have been at the forefront of creating safety and reliability in automotive wiring for all these scenarios, with an overall goal of longer vehicle life expectancy.
The Roles of General Purpose Sleeving
Automobile manufacturers rely on Techflex® general purpose braided sleeving for both wire protection and customization, on the top and sides of the motor, where conditions frequently run cooler. Flexo® PET is one of the Techflex® sleeve types used for abrasion protection in automotive wire applications. Black tends to be the color of choice to blend in with wiring, but Flexo® PET also comes in a wide selection of colors and patterns, making it appropriate for harness customization. Flexo® F6® is another split braided sleeve providing basic abrasion protection for wires, hoses, and tubes. Clean Cut® offers the highest coverage in a standard sleeving configuration for harness applications. It is constructed with fray resistant materials that can be trimmed to size with standard scissors. F6® Woven Wrap is another split loom used in electronic communication and power system wiring — applications that call for added abrasion resistance and elasticity. Flexo® Tight Weave™ has been utilized in automotive harness applications too when fuller coverage is required.
Sleeving for Higher Temperatures and Voltages
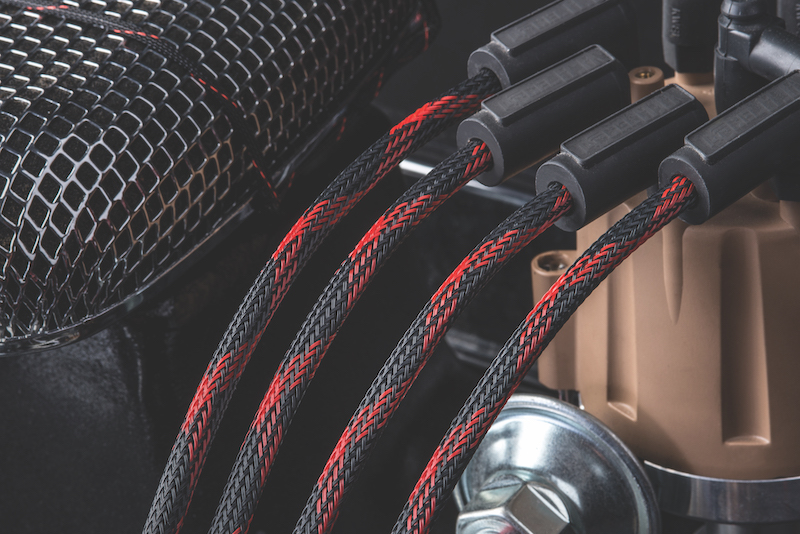
Vehicle manufacturers that especially focus on electric vehicles often seek wire protection to regulate temperatures within batteries and other systems. The Insultherm® product line is one of the high temperature sleeving options from Techflex® auto makers trust to keep temperatures down in extreme heat compartments. It features tightly braided fiberglass that can safeguard harnesses in conditions up to 1,200°F. ThermaShield® products combine fiberglass with an aluminized covering to deflect heat up to 1,400°F. FireFlex® sleeving is a choice for fuel lines and other high heat automotive areas. It is comprised of a silicone skin over fiberglass that safeguards against extreme heat, constant temperatures of 500°F, open flame, and automotive chemicals. It is abrasion and puncture resistant, yet flexible enough to follow tight radius curves.
High voltage cables are one of the concerns with EV wiring. Special protection is a must, particularly if an electric vehicle is ultimately involved in a collision. EV cables can create dangerous conditions on an accident scene for emergency crews. It is the primary reason EV high voltage cables are color coded, with orange the designated color. This identification system can help first responders recognize and avoid these wires, then safely de-energize a vehicle. Techflex® has developed heavy duty Battle Braid® and F6® Battle Wrap in response to EV manufacturer product requests. These sleeves are each constructed with impact resistance and cut through protection, both important aspects in keeping essential EV cables shielded from harm, extending the life of the vehicle and its systems.
Shielding and Specialty Sleeves
Metal and shielding sleeving can also assist with grounding. Flexo® Tinned Copper and Flexo® Tinned Copper Flat are two of the products Techflex® has developed that are useful for shielding and grounding in electrical automotive applications. Flexo® Copper is braided with 100% copper to maintain optimal current transmission. This sleeving category is additionally important in these high-tech vehicles, which may be vulnerable to electromagnetic interference (EMI), radio frequency interference (RFI), and electrostatic discharge (ESD). Automotive engineers from some companies have worked with Techflex® to troubleshoot electrical interference issues at the OEM application level, after obstacles cropped up within complex electrical systems and wiring. Sleeves like Flexo® Shield have resolved EMI complications detected during the vehicle manufacturing processes.
An EV is known for its ability to run almost silently, with an absence of combustion and exhaust keeping its sound levels down. The Techflex® specialty sleeving category was developed with highly engineered, application-specific innovative solutions suitable for the EV industry. Higher efficiency vehicle types have fewer moving parts, creating a quieter ride. Additionally, this type of vehicle is designed with the goal of lowered noise levels throughout, including within its compartments. Some aspects of this vehicle class involve complying with national standards to reduce noise pollution. The Environmental Protection Agency (EPA) and National Highway Traffic Safety Administration (NHTSA) in the United States each have their own. The EPA’s Noise Control Act and the Code of Federal Regulations (CFR) Title 40, Part 205 outline the maximum sound level permitted for several vehicle categories. The NHTSA’s Federal Motor Vehicle Safety Standards (FMVSS) No. 141 has limits for vehicles in particular scenarios. The European Union and United Nations Economic Commission for Europe (UNECE) Regulation No. 51 is another example of a noise-related standard European vehicle producers are required to follow. A hard plastic wire covering is not appropriate where manufacturers are attempting to lessen noise. Flexo® F6® Quiet was developed to stop wire harnesses in door panels and dashboards from rattling. F6® Flat is another specialty sleeving product with a self-wrapping, flat design. It is ideal in constrained automotive spaces, such as under carpets and in vehicle headliners, where noise suppression is needed. This flat, self-wrapping sleeving eliminates unsightly bulges in wire runs, to keep cable bundles streamlined.
On the other hand, a tone must be emitted as a safety measure, to alert pedestrians when electric vehicles are approaching. The Pedestrian Safety Enhancement Act (PSEA) and Quiet Car Rule (FMVSS No. 141) are two rules in the United States. UNECE Regulation No. 138 in Europe makes it mandatory to add an Acoustic Vehicle Alerting System (AVAS) in hybrid and electric vehicles. The regulations, of course, for lowered noise and alerting systems, are other places requiring a separate electrical system. This creates one more location for braided sleeving, with Flexo® PET and Flexo® F6® two options that support the needs for these warning systems, which often necessitate flexibility, abrasion resistance, ease of installation, and acoustic transparency.
Protection for Rodent-Challenged Wiring
Many newer cars and trucks have been equipped with earth-friendly, soy-based wire insulation. Though better for the planet, this component has presented greater challenges to automotive manufacturers, transforming wiring into a potential rodent attractant. Flexo® Rodent Resistant is one of the Techflex® heavy duty braided sleeving products embraced by the automotive industry because it is intended to repel rodents. It is manufactured with proprietary components that make it less appealing to uninvited animals drawn to nibbling on wires.
The Future of Automotive Sleeving Protection
As new facets within the automotive industry develop, Techflex® looks forward to continually partnering with vehicle manufacturers in providing sleeving solutions for every aspect of wire harness protection.
Techflex® has been engineering and manufacturing a wide range of braided sleeving products since 1965. In addition to working with vehicle producers, high performance automotive enthusiasts have sought out Techflex® for its wire, hose, and cable bundling protection solutions. Techflex® has also become known for its sleeving used in a range of other industries, from biomedical to aerospace. The company’s experience with this broad market, and wide selection of general purpose and high-tech specialty products, has made Techflex® the first name in sleeving solutions. www.Techflex.com.